Self-vulcanising tape, often referred to as self-fusing or self-amalgamating tape, is an essential product in the toolbox of both seasoned professionals and DIY enthusiasts. Its unique properties make it a versatile and reliable solution for a variety of applications, setting it apart from conventional adhesive tapes.
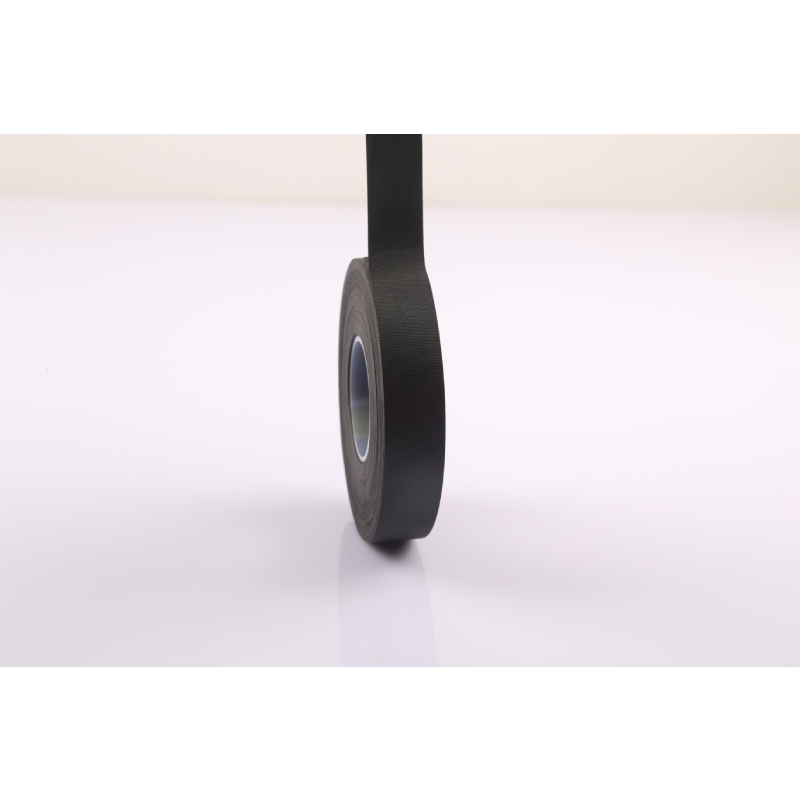
Having over two decades of experience in electrical engineering, I have found self-vulcanising tape to be incomparable in situations requiring robust, long-lasting insulation and protection. Unlike regular adhesive tapes, this tape doesn’t rely on sticky resin but on a process called vulcanisation to bond to itself. When stretched and wrapped around a material, its polymer structure begins to merge and fuse, creating a seamless layer that is resistant to water, heat, and even certain chemicals. This capability is crucial for applications that demand durability and watertight sealing, such as in electrical cable splicing and underwater repairs.
The expertise required to fully leverage self-vulcanising tape extends beyond simple application. As with any professional tool, understanding its limitations is as important as knowing its benefits. For optimal effectiveness, it is crucial to apply the tape correctly under the right conditions. Clean, dry surfaces ensure the tape fuses properly without any hindrance. Stretching the tape to up to twice its length before application ensures a tighter, more secure bond. Through years of field work, I have seen the difference meticulous preparation can make in the tape's performance.
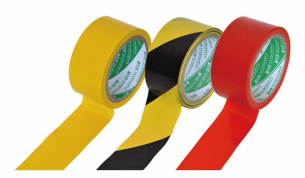
Recognition of self-vulcanising tape’s authoritativeness comes from its widespread adoption across multiple industries. Whether in marine settings for preventing corrosion, in electrical installations for insulation, or mechanical repairs to seal leaks and reinforce structural weaknesses, its resilience has been proven time and again. Such widespread acceptance is a testament to its reliability and efficiency. Additionally, it is invaluable during emergency repairs in remote locations where more sophisticated solutions are unavailable. This versatility has made it a staple recommendation for various industry standards and practices.
self vulcanising tape
However, the tape’s trustworthiness is not only born from professional use but also from its adherence to strict safety standards. Many self-vulcanising tapes are reviewed and certified to conform to international safety regulations, ensuring that it provides a safe user experience. During my career, I have witnessed the profound impact of these certifications on the adoption of this product across infrastructure projects. These certifications provide assurance not just to professionals but to aspiring DIYers who rely on the tape for personal use projects.
For those venturing into the use of self-vulcanising tape, it is worthy to consider the specifications particular to their project. Factors such as temperature resistance, tensile strength, and resistance to UV are critical in ensuring the selected tape aligns with specific project needs. There are variations available tailored to meet these requirements, which can be crucial in ensuring the longevity and success of your application. Product datasheets often reveal these attributes, and consulting them, along with customer reviews and official guidelines, is paramount to making a sound decision.
To conclude, the self-vulcanising tape has established itself as a product of high reliability and utility in multiple sectors. Through proper application and understanding of its properties, it offers unmatched performance. Keeping abreast of its latest developments and adhering to best practices in its deployment ensures that users can maximize its benefits while maintaining safety and compliance. Its enduring presence in the market is not merely due to its functionality but also thanks to the authoritative backing by experts and the trust it has built through consistent, proven outcomes.