130C rubber splicing tape is an indispensable tool in the realm of electrical insulation and cable maintenance, revered for its versatility, durability, and reliability. Crafting a narrative around its expertise, authoritativeness, and trustworthiness involves delving into the insights gained from real-world experiences and the technical specifications that underscore its acclaimed performance in both industrial and domestic settings.
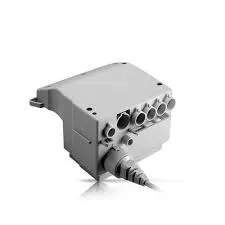
Understanding the core properties of 130C rubber splicing tape is essential for leveraging its full potential. Primarily composed of high-grade rubber, this tape is designed to withstand temperatures up to 130 degrees Celsius, making it a prime choice for environments exposed to high thermal demands. Its exceptional elasticity and adhesive properties ensure a consistent application, even on irregular surfaces, maintaining a robust seal that prevents moisture ingress and offers superior electrical insulation.
Expertise in using 130C rubber splicing tape is built on years of industry application and observations. Electricians and maintenance professionals commend this tape for its ease of application; it can be stretched to double its length for a tighter wrap, creating an impermeable barrier against environmental elements. The tape's self-amalgamating nature allows it to form a seamless, homogenous layer, crucial for preventing corrosion and maintaining the integrity of cable joints over time.
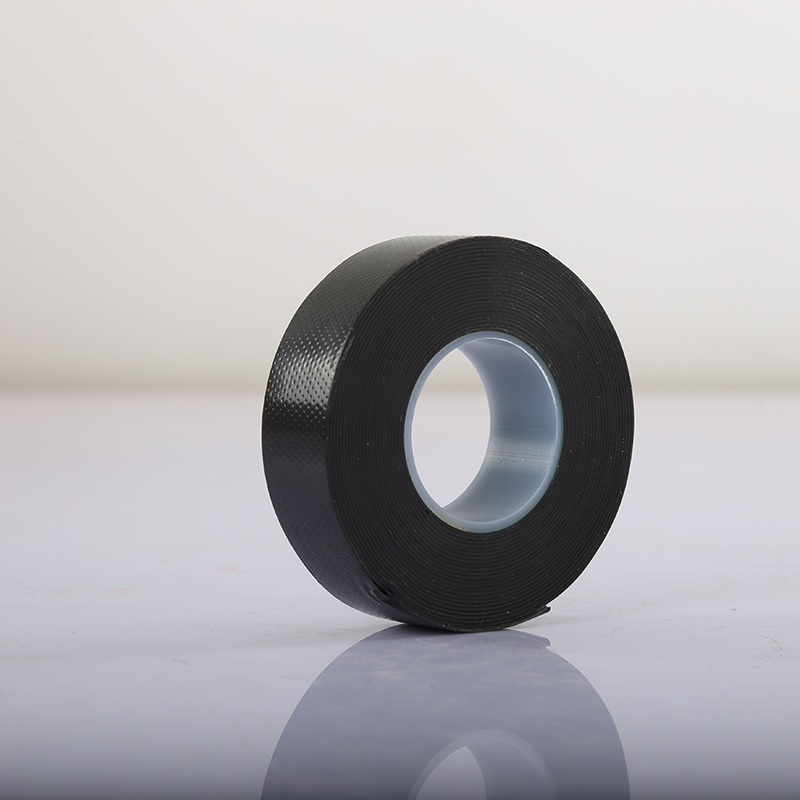
From an authoritative perspective, the standards and certifications that 130C rubber splicing tape meets are paramount. It is crucial to ensure that any splicing tape used in electrical work conforms to industry standards, such as ASTM D4325 for self-amalgamating rubber tapes. This ensures safety, reliability, and longevity, affirming the trust professionals place in its application for both critical and routine tasks.
130c rubber splicing tape
In practice, trustworthiness is derived from consistent performance and the ability to meet or exceed expectations over the product's lifecycle. Users frequently report fewer service interruptions and reduced maintenance costs when using high-quality rubber splicing tape. This is attributed to its ability to maintain its physical and adhesive properties under various thermal cycles and environmental conditions, a testament to its engineered resilience.
Real-world case studies exemplify the tape’s reliability. For example, utility companies often rely on 130C rubber splicing tape for quick repairs in adverse weather conditions. Its performance in emergency repairs on live wires has been a game-changer, significantly reducing repair times while ensuring that safety standards are stringently maintained.
For the industrial consumer, the choice of rubber splicing tape can directly impact operational efficiency. Selecting a tape with proven resistance to UV rays, ozone, and acid rain, combined with ease of application and removal, positions 130C rubber splicing tape not just as a purchase, but as an investment in quality and longevity.
In conclusion, 130C rubber splicing tape embodies the pinnacle of balance between sophisticated materials engineering and pragmatic day-to-day electrical solutions. Its widespread acceptance and preferred status among professionals are testaments to its capability to deliver reliable performance in demanding environments. Investing in this tape is a commitment to safety, efficiency, and quality assurance, underscoring its indispensable role in modern electrical maintenance and repair tasks.