Rubber splicing tape, a crucial component in various industries, has become increasingly significant due to its versatility and effectiveness. This specialized tape is primarily composed of rubber or a rubber-like material, offering exceptional elasticity and adhesion. Its primary function is to join or repair materials where flexibility and resilience are paramount.
The 23% rubber splicing tape specifically refers to the proportion of rubber content within the tape, indicating a high concentration that ensures enhanced performance. This particular blend offers a balance between cost-effectiveness and durability, making it suitable for applications requiring moderate elasticity and bond strength. The rubber content contributes to the tape's overall stretchiness, allowing it to conform to irregular surfaces and absorb shocks or expansions without peeling off or breaking.
In the realm of industrial applications, 23% rubber splicing tape is often used in the automotive industry for electrical insulation and sealing, where its elastic properties prevent damage from vibrations. It's also prevalent in construction, especially for waterproofing and sealing roofs and pipes, as well as in the aerospace industry for lightweight, flexible connections.
Beyond functionality, the use of 23% rubber splicing tape raises environmental concerns. Rubber, particularly synthetic varieties, can be non-biodegradable, posing disposal issues Rubber, particularly synthetic varieties, can be non-biodegradable, posing disposal issues
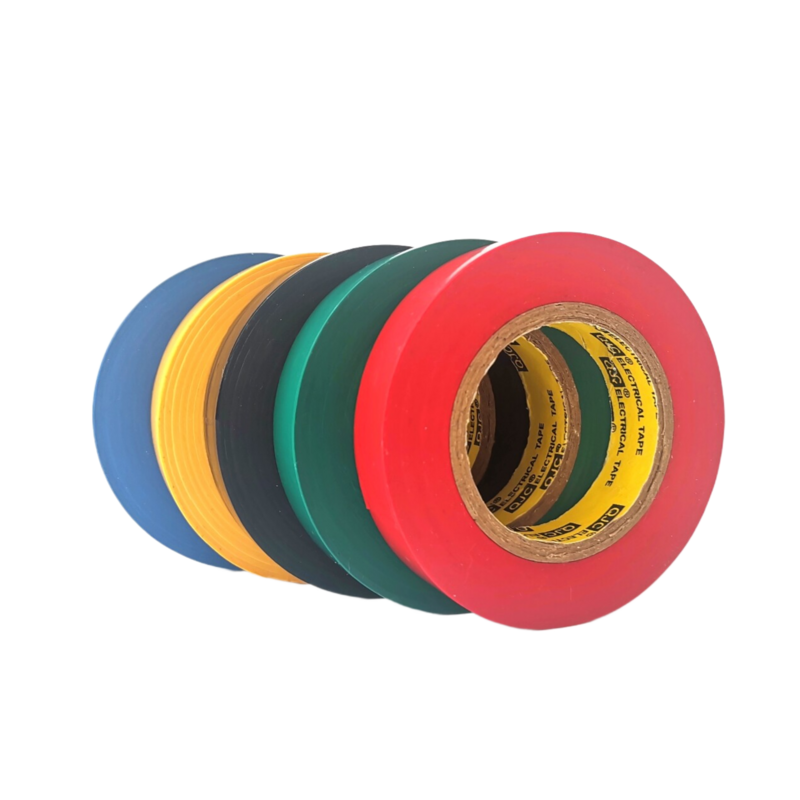
Rubber, particularly synthetic varieties, can be non-biodegradable, posing disposal issues Rubber, particularly synthetic varieties, can be non-biodegradable, posing disposal issues
23 rubber splicing tape. However, advancements in recycling technologies and the development of more eco-friendly rubber compounds are mitigating these concerns. Moreover, the energy efficiency gained from using such tapes in insulation often offsets their production environmental impact.
From a technical perspective, the production process of 23% rubber splicing tape involves mixing raw rubber with other polymers and additives to achieve the desired elasticity and bonding capabilities. This mixture is then calendered into thin sheets and cut into tapes of various widths and lengths. The quality control in this process ensures that each tape meets industry standards for stretching, adhesive strength, and durability under different temperatures and conditions.
In conclusion, 23% rubber splicing tape represents an important innovation in industrial materials, offering a balance of cost, performance, and reliability. As technology continues to evolve, so too will the applications and environmental considerations surrounding this essential tape. Its versatility and efficacy ensure that it remains a staple in numerous sectors, overcoming challenges through adaptability and innovation.