In the ever-evolving field of electrical insulation, liquid rubber has emerged as a standout solution, offering unparalleled benefits for both residential and industrial applications. This article delves into the unique properties and applications of liquid rubber electrical insulation, drawing on real-world experiences and expert insights to highlight its role as a groundbreaking material in the industry.
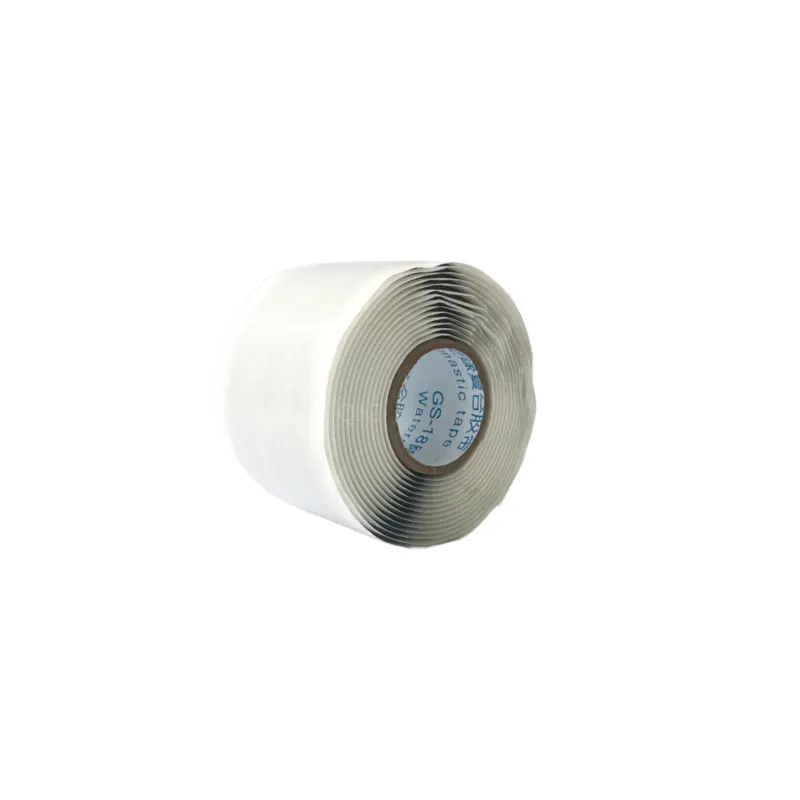
Liquid rubber, a versatile and adaptable compound, has been gaining traction for its exceptional capabilities in electrical insulation. Unlike traditional materials, liquid rubber offers a seamless application process, adhering to surfaces with ease and forming a robust, continuous layer that protects electrical systems. Its flexible nature allows it to accommodate movements and vibrations, which are common in dynamic electrical environments, without compromising on insulation quality.
One of the key experiences shared by industry professionals is the ease of application. Liquid rubber can be applied using a simple brush, roller, or spray method, making it accessible for various projects, from DIY home insulation to elaborate industrial installations. Users have noted the material's ability to form a tight bond over uneven surfaces, filling gaps and ensuring comprehensive coverage. This application process not only saves time but also reduces labor costs, making it an economically viable option for many.
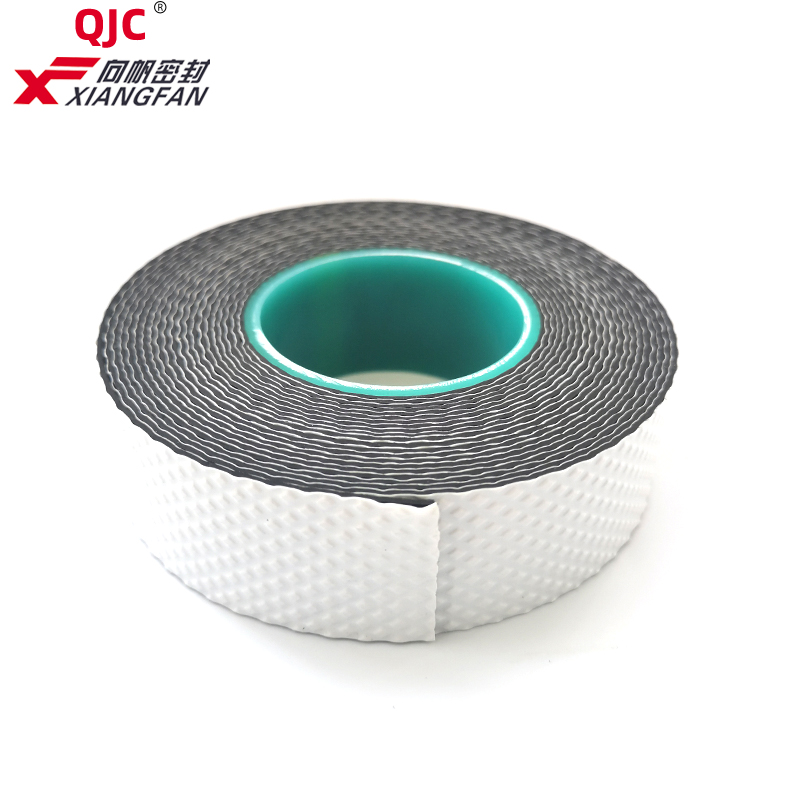
Experts underscore the material's superior protective qualities. Liquid rubber demonstrates excellent resistance to environmental factors such as moisture, chemicals, and UV radiation. This resistance ensures that once applied, the insulation remains effective for extended periods, safeguarding electrical components from potential damage and reducing maintenance costs. This durability is particularly valuable in outdoor or harsh industrial settings, where traditional insulation materials may degrade more rapidly.
liquid rubber electrical insulation
From a technical perspective, liquid rubber's molecular structure is engineered to provide high dielectric strength, an essential characteristic for preventing electrical leakage and ensuring safety. This high dielectric strength, combined with its thermal stability, makes liquid rubber an ideal choice for insulating high-voltage or high-temperature equipment. As a result, industries such as power generation, automotive, and telecommunications are increasingly utilizing liquid rubber for its reliable performance under demanding conditions.
Trustworthiness is a crucial aspect when evaluating insulation materials, and liquid rubber's track record speaks volumes. Companies that have adopted liquid rubber insulation report significant reductions in system failures and enhanced operational efficiency. These results have been supported by comprehensive testing and certification by recognized bodies, ensuring compliance with international safety and quality standards.
Moreover,
the adaptability of liquid rubber extends to its environmental impact. Many formulations are designed to be environmentally friendly, featuring low VOC (volatile organic compound) content and non-toxic properties. This focus on sustainability not only aligns with global trends toward eco-conscious practices but also provides peace of mind for users concerned about the environmental impact of their projects.
In conclusion, liquid rubber electrical insulation represents a significant advancement in insulation technology. Its unique blend of ease-of-use, durability, and superior protective qualities makes it a preferred choice among professionals and homeowners alike. With proven effectiveness across a range of applications, liquid rubber offers a trusted and authoritative solution, setting new standards in electrical insulation. As industries continue to prioritize safety, efficiency, and sustainability, liquid rubber is poised to play a central role in the future of electrical insulation materials.