The Evolution and Impact of Butyl Rubber Tape Manufacturers
In the vast landscape of industrial adhesives and sealants, butyl rubber tape stands out for its unparalleled properties and versatility. This unique material, crafted by specialized manufacturers worldwide, has revolutionized how we approach waterproofing, gasketing, and sealing in various industries. From construction to automotive, from electrical insulation to HVAC systems, butyl rubber tape has become an essential component, ensuring durability and protection against the elements.
Butyl rubber tape manufacturers have perfected the science behind this remarkable product, blending innovation with traditional manufacturing techniques. The butyl rubber itself is a copolymer of isobutylene and isoprene, offering exceptional impermeability to gases and excellent resistance to moisture, extreme temperatures, ozone, and UV radiation. This chemical composition makes butyl rubber tape an ideal choice for applications requiring long-term reliability without degradation.
Manufacturers of butyl rubber tape invest heavily in research and development to maintain their edge in the industry. They continuously explore new formulations that enhance the performance of the tape, making it even more adaptable to diverse environments and application needs. For instance, some have developed butyl tapes with enhanced adhesion or modified thicknesses to cater to specific customer requirements.
The production process of butyl rubber tape is a testament to precision and quality control. It begins with the careful selection of raw materials, followed by compounding, where the butyl rubber is mixed with other ingredients to achieve the desired properties. The next step involves calendering, a process through which the rubber is formed into thin sheets The next step involves calendering, a process through which the rubber is formed into thin sheets
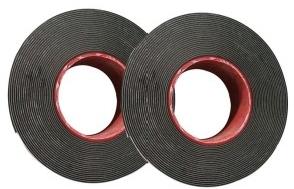
The next step involves calendering, a process through which the rubber is formed into thin sheets The next step involves calendering, a process through which the rubber is formed into thin sheets
butyl rubber tape manufacturers. These sheets are then converted into tapes of various widths and thicknesses, cut with precision, and wound onto spools for distribution.
Butyl rubber tape manufacturers also place a strong emphasis on sustainability and environmental stewardship. They strive to reduce their ecological footprint by implementing eco-friendly production methods and sourcing renewable materials whenever possible. Additionally, they ensure that their products meet international standards and regulatory compliances, guaranteeing safety and efficacy across borders.
As technology advances, so too does the capability of butyl rubber tape manufacturers to innovate. With the integration of smart manufacturing technologies and automation, these producers can now offer more consistent and higher-quality products than ever before. They are also able to customize their tapes further, catering to niche markets and emerging industries with specific needs.
In conclusion, butyl rubber tape manufacturers play a pivotal role in maintaining the integrity of various sectors by providing a reliable solution for sealing and protecting against the harshest of elements. Their commitment to excellence, innovation, and sustainability ensures that this essential material continues to evolve, meeting the demands of an ever-changing world.