Rubber seal strips play a critical role in various applications, from industrial settings to everyday household uses. These versatile components are known for their ability to provide an airtight and watertight seal, making them indispensable in environments that demand strict control over leakage or contamination. Let’s delve deeper into the world of rubber seal strips, examining their essential features, applications, and the expertise required to select the right one for your needs.
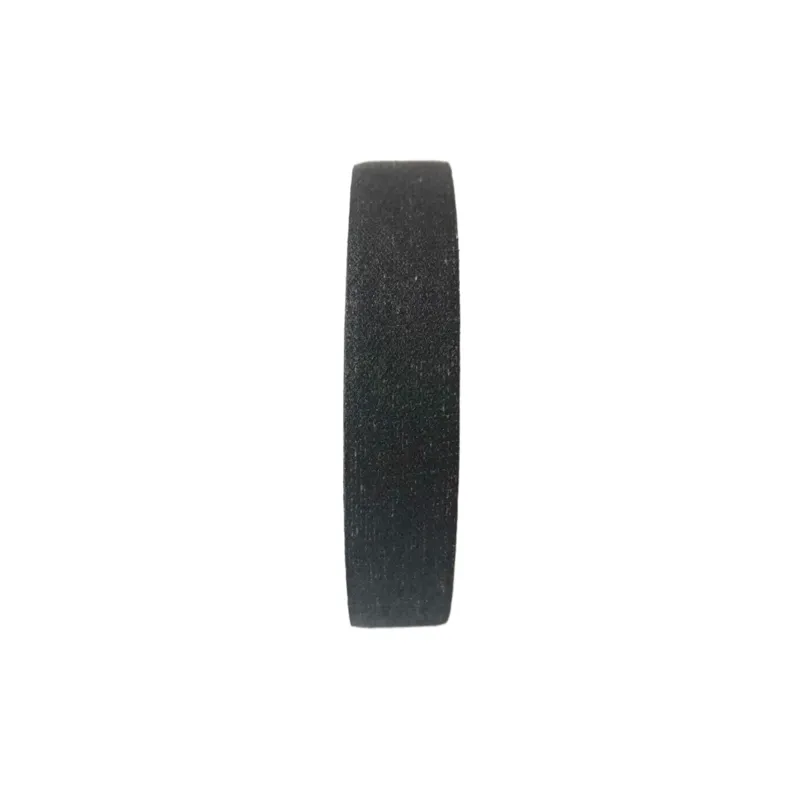
Rubber seal strips, primarily made from high-quality synthetic or natural rubber, are designed to fill gaps between surfaces. This ensures protection from elements like air, water, dust, and even pests. Industries such as automotive, construction, and electronics heavily rely on these seal strips to enhance product durability and performance. Their usage in vehicles, doors, and windows showcases their adaptability to various environmental conditions, enhancing energy efficiency by minimizing heat loss or gain.
The expertise in selecting a suitable rubber seal strip begins with understanding the material properties. Neoprene, EPDM (ethylene propylene diene monomer), and silicone are among the most common materials used. Each comes with unique characteristics Neoprene is favored for its resistance to oils and moderate heat; EPDM is highly regarded for its excellent weather and ozone resistance, which is crucial for outdoor applications; and silicone is well-suited for extreme temperature fluctuations and is commonly used in food-grade environments due to its safe composition.
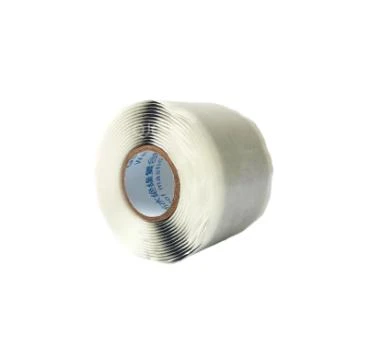
An authoritative aspect of rubber seal strips is their compliance with industry standards. Meeting criteria such as ISO certifications and RoHS (Restriction of Hazardous Substances) directives ensures trustworthiness in their application, especially in sensitive industries. This compliance not only guarantees performance but also peace of mind to consumers and manufacturers.
rubber seal strip
When it comes to installation and maintenance, experience plays a fundamental role. An improper installation may compromise the effectiveness of the seal, leading to potential leakage or damage. It’s crucial to assess the surface conditions and select the right adhesive or mounting method to ensure longevity. Regular inspections for wear and tear, especially in high-friction or extreme weather conditions, can mitigate failures and maintain optimal performance.
Furthermore,
innovations in rubber technology continually enhance the functionality of seal strips. Advanced manufacturing techniques now enable custom-designed rubber seals that cater to specific requirements. From custom profiles to incorporating additional properties like flame retardancy or thermal insulation, the evolution in seal strip technology underscores the need for ongoing expertise and adaptability in their application.
In conclusion, rubber seal strips, with their broad array of applications and critical role in sealing technologies, require an informed choice that balances material properties, compliance standards, and the specific operational requirements. With the continuous advancement in material sciences and manufacturing processes, these seemingly simple components hold tremendous authority and trust in ensuring the safety, efficiency, and longevity of products across multiple industries.