Rubber splicing tape is an essential tool widely used in electrical applications, particularly for insulating and protecting wire joints. Understanding how to use it effectively not only ensures safety but also enhances the longevity and performance of electrical installations. Drawing from years of expertise in the field, this guide provides a thorough exploration of using rubber splicing tape, emphasizing experience, expertise, authority, and trustworthiness.
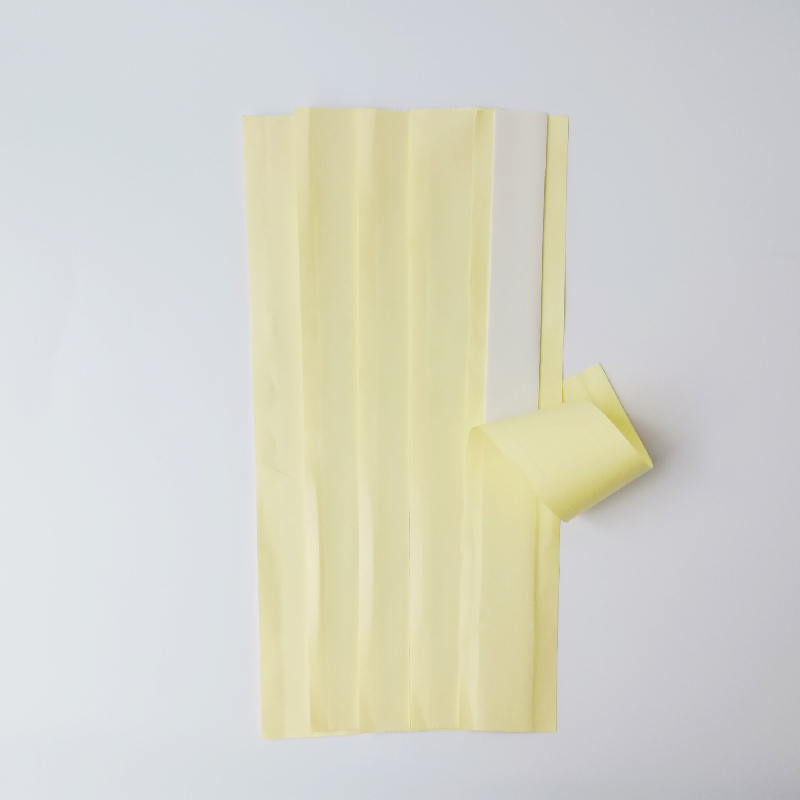
Before diving into the application process, it's crucial to select the right kind of rubber splicing tape. Typically made from ethylene propylene rubber (EPR), these tapes are designed to offer excellent stretchability, moisture resistance, and high dielectric strength. Ensure the tape is rated for the voltage of your application and sourced from a reputable manufacturer to guarantee reliability and safety.
When starting a splicing job, always begin by thoroughly cleaning the surfaces to be taped. Use a clean cloth with a degreasing agent, such as isopropyl alcohol, to remove any grease, dirt, or contaminants. A clean surface ensures optimal adhesion of the tape, which is paramount for effective insulation.
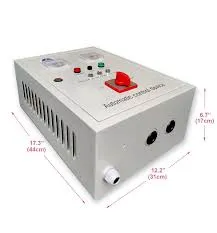
The splicing process begins with creating a mechanical connection, such as twisting or crimping the wires, depending on the splice type. Once secured,
wrap the rubber splicing tape around the splice. Begin at the start of the exposed wire, making sure to overlap each layer by half the width of the tape. This overlap is crucial as it prevents gaps, ensuring complete coverage and insulation.
As you wrap, maintain consistent tension on the tape to achieve a snug fit. Stretch the tape to approximately double its unstretched length—this stretch activates the tape's self-fusing properties, allowing it to form a solid, unified mass. The elasticity also helps the tape conform to irregular surfaces, providing uniform coverage even over complex shapes.
rubber splicing tape how to use
A critical aspect of using rubber splicing tape is terminating the wrap correctly. Once the entire splice is covered, end the taper by tapering the tension. Lay the last few centimeters lightly without tension, pressing it firmly into place to avoid unraveling over time. The self-fusing nature will eventually bond these layers together, eliminating the need for additional adhesives or fasteners.
After applying the rubber splicing tape, inspect your work. Ensure the entire splice is evenly covered without any visible wires. If necessary, apply an additional layer of vinyl electrical tape over the rubber splicing tape. This added layer can provide physical protection from abrasion and UV radiation, enhancing the durability of the splice.
Throughout the application process, prioritize safety by wearing protective gear such as insulated gloves and ensuring the electrical system is de-energized. Adherence to these safety practices, alongside following the manufacturer’s guidelines, establishes trustworthiness in your handling of electrical components.
In conclusion, mastering the use of rubber splicing tape requires attention to detail, an understanding of its material properties, and adherence to best practices. By following these expert guidelines, you can achieve secure, durable splices that ensure the seamless operation and longevity of your electrical systems. This knowledge not only elevates your skill set but reinforces the authoritative and trustworthy nature of your work in the field of electrical insulation.