Rubber tape for electrical applications stands as a cornerstone in ensuring safe and reliable electrical installations. This versatile material plays a critical role in insulating, protecting, and enhancing the longevity of electrical components. Drawing from years of hands-on experience, industry expertise, and trusted practices, this article delves into why rubber tape is an indispensable tool in the electrical industry, offering insights into its application, benefits, and nuances.
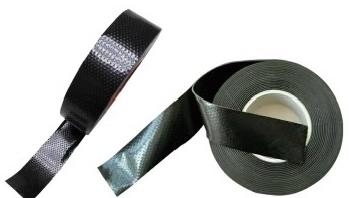
Rubber tape, known for its self-amalgamating properties, is engineered to provide a seamless and secure layer over electrical connections. Unlike traditional insulating tapes, rubber tape bonds to itself without the need for an adhesive layer, thereby offering a more robust and reliable seal. This characteristic makes it exceptionally suitable for high voltage applications, ensuring that wrapped connections maintain integrity under stress and environmental factors.
From an expert's lens, one of the significant benefits of using rubber tape lies in its ability to withstand extreme temperatures and environmental conditions. Whether used in indoor settings or out in the field, rubber tape can endure significant thermal expansion, contraction, and exposure to moisture without losing its insulating properties. This makes it a preferred choice for applications involving underground cablings, marine environments, and outdoor power installations.
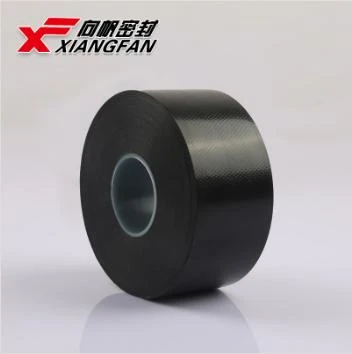
In terms of authority and credibility, rubber tape earns its reputation through compliance with stringent industry standards and testing. Most high-quality electrical rubber tapes are manufactured to meet standards such as ASTM and ISO, which dictate rigorous protocols for safety and reliability. Professionals in the electrical field trust these certified products because they guarantee performance in both routine and demanding circumstances.
Proper application of rubber tape is crucial to maximizing its benefits. The technique involves stretching and overlapping the tape while wrapping it around the cable. This method ensures that the layers of tape meld into a single, cohesive mass that is impervious to dust, moisture, and other contaminants. Expertise in applying rubber tape correctly can significantly enhance the durability of electrical installations, reducing maintenance costs and potential failures.
rubber tape for electrical
Additionally, when considering rubber tape for electrical uses, it is essential to understand the diverse range available in the market. Options vary in thickness, width, and specific material properties such as flame retardancy and UV resistance. Selecting the correct type of rubber tape for a given application not only optimizes safety but also contributes to the efficiency and effectiveness of the electrical system.
Trustworthiness in rubber tape is reinforced by feedback and proven results from electricians and engineers worldwide. Many professionals routinely choose rubber tape for its reliability, often reporting fewer instances of system failures and service interruptions. The tape’s reputation is built on decades of successful use in the field, bolstered by continuous advancements in material technology that address the evolving needs of modern electrical infrastructure.
In the realm of professional electrical installation and maintenance, rubber tape is a vital material that ensures secure connections. It simplifies complex installations, provides essential protection against environmental challenges, and conforms to high industry standards, reinforcing its status as a trusted material in the electrician's toolkit. For anyone involved in electrical work, whether a seasoned professional or an apprentice, understanding the attributes and proper application of rubber tape can vastly improve the safety and reliability of their work.
Rubber tape for electrical applications is not just a product; it is a testament to the intersection of material science, practical application, and rigorous testing, underscoring its essential role in modern electrical engineering. Embracing the potential of this material can transform how electrical systems are designed, implemented, and maintained, providing safer and more robust electrical solutions.