Self-amalgamating tape is a remarkable innovation in the realm of electrical insulation and repair, particularly praised for its performance across various temperature conditions. Its utility in maintaining secure, insulated connections in electrical systems makes it indispensable for electricians and DIY enthusiasts alike. With advancements in engineering materials, self-amalgamating tape has transitioned from a specialized tool into a mainstream product, accessible to both professionals and hobbyists. However, its effectiveness can be heavily influenced by temperature, which is a critical aspect often misunderstood.
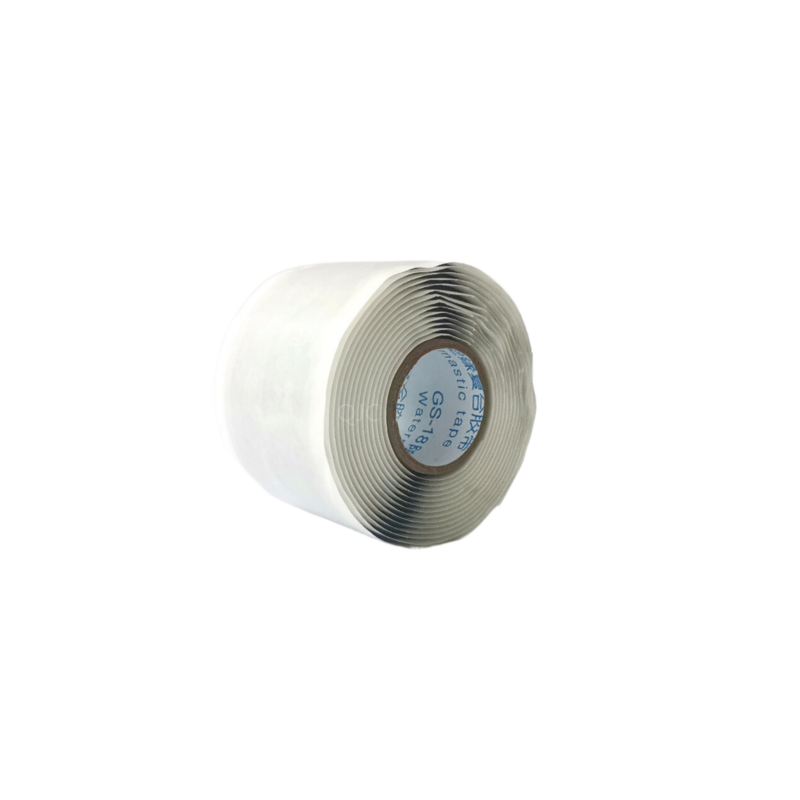
One of the primary reasons self-amalgamating tape is favored is its unique ability to bond to itself without needing any adhesive. Its performance is predominantly derived from the silicone or ethylene propylene rubber composition, which reacts under tension, creating a cohesive bond. This feature is incredibly beneficial in providing a water-tight seal and an airtight barrier, crucial for electrical splicing and insulation tasks. When temperature is introduced into the equation, the product's composition means it must maintain stability from extreme cold to blazing heat.
Performance in Temperature Extremes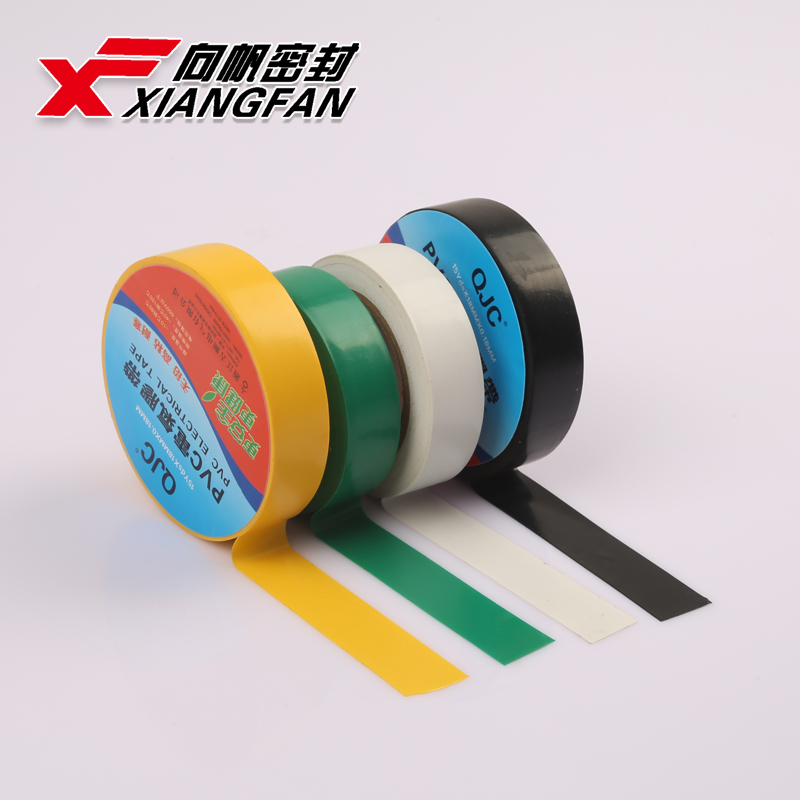
1. Cold Climates In regions where temperatures regularly drop below freezing, self-amalgamating tape continues to exhibit remarkable resilience. Its elastomeric properties allow it to resist becoming brittle or cracking, which is a common downfall of many insulating materials. Even under icy conditions, the tape remains flexible and maintains its adhesiveness, making it an ideal solution for outdoor electrical wiring.
2. Hot and Humid Environments The other end of the spectrum presents its own set of challenges. In high temperatures, especially those exceeding 150°C (302°F), the tape's material must resist deformation and maintain its sealing abilities. Renowned brands, through rigorous testing, offer variants specifically designed to withstand such heat without compromising effectiveness. Humidity adds another layer of complexity, but self-amalgamating tapes excel because they are inherently water-resistant and repel moisture.
3. Thermal Cycling In environments where temperatures swing drastically—think industrial settings or geographical locations with fluctuating climates—self-amalgamating tape showcases exceptional durability. Continuous bonding and reliable performance under thermal cycling conditions demonstrate why it is the go-to for temporary and semi-permanent electrical repairs.
self amalgamating tape temperature
Expert Tips for Optimal Use
- Surface Preparation Ensure that the surface is clean and dry to maximize the tape's self-bonding capability. Any oils, dirt, or residue can hinder the process, particularly in low temperature scenarios where the tape might naturally contract slightly.
- Proper Wrapping Techniques Overlapping the tape by at least 50% of its width during application ensures comprehensive coverage and insulation. Especially in high-temperature situations, this technique mitigates the risk of gaps forming due to expansion.
- Layering for Insulation To enhance thermal insulation, especially in outdoor electrical applications exposed to prolonged sunlight or cold, apply multiple layers. Each additional layer serves as a thermal barrier.
Manufacturers have recognized the importance of tailoring self-amalgamating tape to cater to specific temperature requirements. Consequently, selecting the appropriate type based on temperature considerations is crucial for maximizing application success.
In conclusion, self-amalgamating tape's popularity is largely due to its adaptability across temperature extremes. Testing and expert formulation ensure that, regardless of ambient conditions, it remains a highly reliable method for securing and insulating electrical connections. Understanding the effect of temperature and employing best practices in application can dramatically enhance its efficiency and longevity, cementing its reputation as an indispensable tool in both professional and domestic settings. As technology evolves, continued innovations promise even greater resilience, ensuring this versatile tool remains at the forefront of industrial materials.