In the world of automotive engineering, the seemingly mundane component known as the wiring loom wrap plays an understated yet crucial role in ensuring a vehicle’s electrical system operates smoothly and safely. As an integral part of automotive electrical systems, the wiring loom wrap serves multiple purposes, offering protection, organization, and reliability to the intricate networks of wires that power modern vehicles.
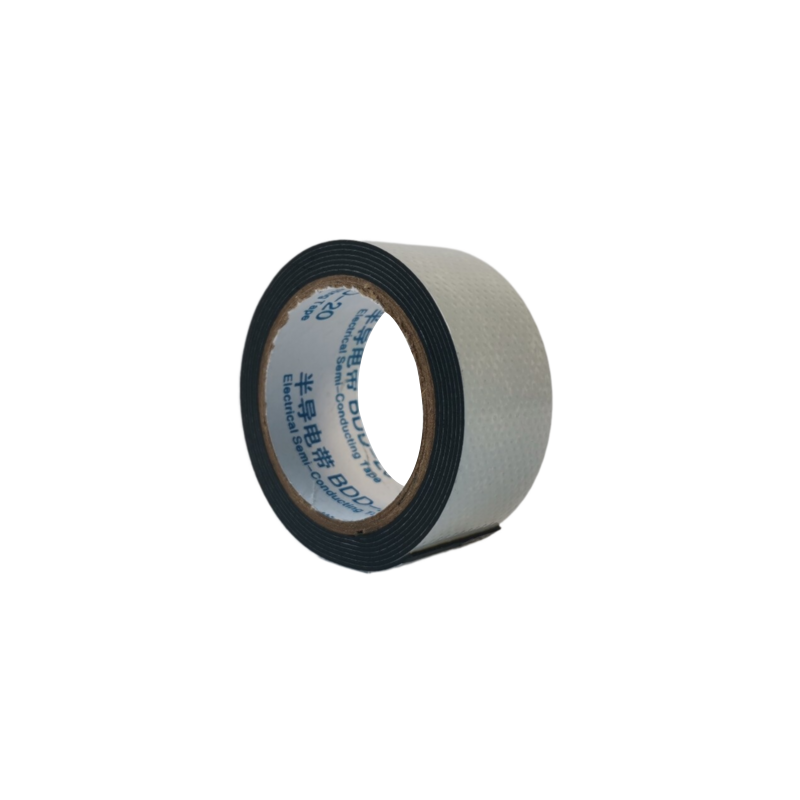
Automotive wiring loom wraps are designed to meet the demanding requirements of today's complex vehicles, where electrical systems control everything from engine functions to advanced driver-assistance systems. The effectiveness of a wiring loom wrap can directly impact the performance and safety of these systems, making it a critical component for automotive manufacturers and repair professionals alike.
One of the primary benefits of a wiring loom wrap is its protective function. The wires within a vehicle are vulnerable to a range of environmental factors such as heat, abrasion, and chemical exposure. A high-quality loom wrap provides a protective shield, helping to prevent damage from these external factors. This is particularly important in high-temperature areas of the engine bay, where specialized materials like flame-retardant polyester wraps can withstand extreme conditions and prevent the risk of fire or wire insulation failure.
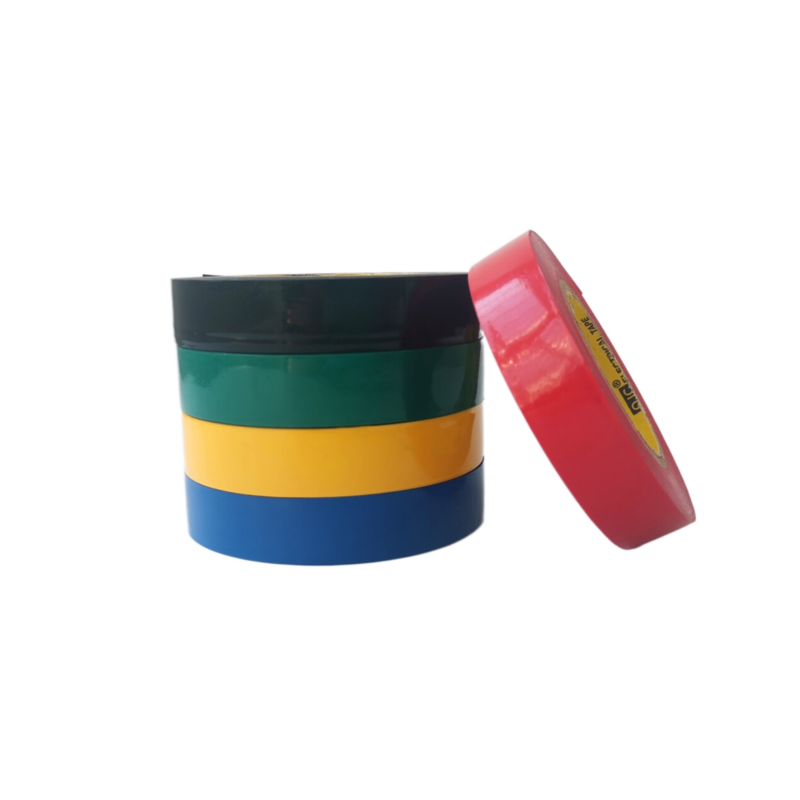
Moreover, the organization provided by an automotive wiring loom wrap cannot be overstated. Without a structured arrangement, the multitude of wires within a vehicle can become tangled, leading to misconnects or shorts that can compromise system performance. Well-designed wraps ensure each wire remains in its designated group, reducing the likelihood of installation errors and simplifying future maintenance or upgrades. The neat organization also aids in visual inspections and diagnostics, making it easier to track down issues without unraveling a chaotic web of cables.
automotive wiring loom wrap
From a professional expertise perspective, selecting the right loom wrap involves understanding the specific environmental and operational demands of the vehicle in question. There are various types of loom wraps available, including braided, spiral, and convoluted tubing, each offering unique advantages depending on the application. For instance, braided wraps are often used for their flexibility and ability to accommodate movement, while convoluted tubing provides robust protection against abrasion.
The authoritativeness of a manufacturer or supplier also plays a significant role in the trustworthiness of wiring loom wraps. Leading automotive OEMs and suppliers invest extensively in research and development to ensure their products not only meet but exceed industry standards. ISO certification can be a marker of quality, indicating that a company adheres to rigorous production processes and quality assurance protocols.
Trust in wiring loom wraps is further bolstered through extensive testing and compliance with automotive standards. These include tests for thermal endurance, chemical resistance, and flexibility, ensuring that products perform reliably under a variety of conditions. A reputable supplier will also provide detailed product specifications and technical support, assisting automotive professionals in making informed decisions that safeguard the integrity of their electrical systems.
Overall, the automotive wiring loom wrap is a vital component that plays a significant role behind the scenes. It contributes to the safety, efficiency, and longevity of a vehicle’s electrical network. Proper selection and application of these wraps not only protect the wires but also enhance the overall reliability of the vehicle, delivering peace of mind to manufacturers, mechanics, and drivers alike. As technological advancements continue to expand the capabilities of automotive electrical systems, the importance of high-quality wiring loom wraps will only grow, reinforcing their status as indispensable elements of modern automotive design and engineering.