When it comes to ensuring the longevity and safety of electrical systems, the role of insulation tape cannot be underestimated. This versatile product, often seen as a toolbox staple, has evolved significantly over the years. Its modern iterations not only enhance protection but also offer innovative features that address specific electrical and industrial needs.
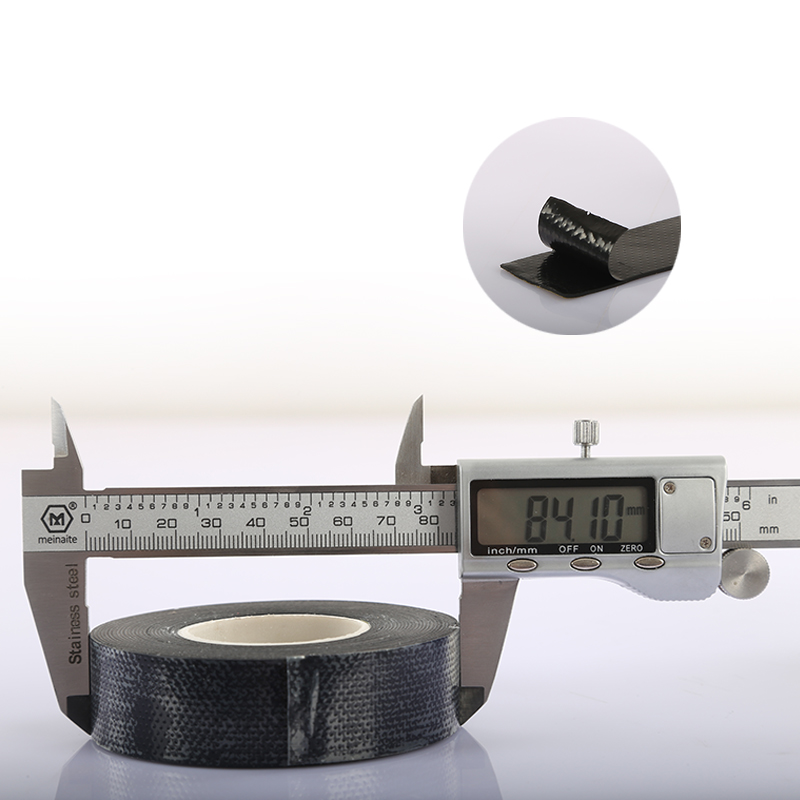
The primary purpose of insulation tape is to insulate electrical wires and other materials that conduct electricity. This prevents electrical currents from accidentally passing to other wires, which can cause short circuits or electrical fires. Constructed from a variety of materials, including PVC, vinyl, and rubber, these tapes are designed to withstand different environmental conditions, from extreme temperatures to moisture and UV light exposure.
One of the standout products in the insulation tape market is the high-temperature resistant tape. Ideal for environments that experience excessive heat, such as factories or vehicles, these tapes maintain their effective adhesive qualities and insulation properties even at elevated temperatures. They are indispensable in settings where standard tape would fail, ensuring uninterrupted operation and safety.
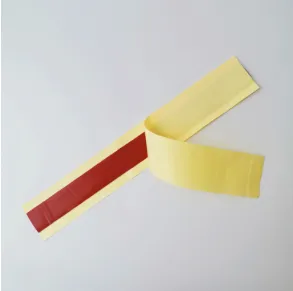
Similarly, waterproof insulation tapes are essential for outdoor applications. These tapes feature a robust adhesive layer that remains intact despite exposure to rain, humidity, or submerged conditions. They are crucial in electrical installations in gardens, outdoor signs, or in marine environments, where persistent moisture is a concern.
Experience has shown that choosing the correct type of insulation tape for specific applications significantly reduces equipment downtime and maintenance costs. Industry professionals emphasize the importance of matching the tape specifications—such as tensile strength and thermal compatibility—to the environment in which it's used. A common misconception is that any tape can be used interchangeably, but experts caution against this. Using the wrong type can lead to severe safety hazards, including insulation failure or even fire hazards.
insulation tape
Furthermore, expertise in the field advocates for the periodic inspection of all tape-insulated components.
This ensures that the adhesive and insulation properties remain intact over time. Seasonal changes and aging can impact the tape's effectiveness. By regularly checking and replacing tape when necessary, the risks of insulation breakage are minimized.
The authoritativeness of insulation tape manufacturers plays a pivotal role in market leadership. Renowned brands often conduct rigorous testing and compliance with international safety standards, such as UL and IEC, to offer products that buyers can trust. These certifications are not mere formalities but are indicative of a product's reliability and safety, providing additional assurance to users who depend on these products in critical applications.
Trustworthiness is further enhanced by transparent practices and clear communication from manufacturers. Providing comprehensive data sheets that outline a tape's capabilities, limitations, and best-use recommendations empowers users to make informed decisions. User testimonials and case studies also contribute to a brand’s credibility, offering real-world evidence of performance across different scenarios.
In conclusion, insulation tape is more than just an ancillary product; it is a critical component of electrical safety and efficiency. A deep understanding of its types, applications, and correct usage ensures not only the safety of electrical systems but also optimizes their performance. For anyone involved in electrical installation or maintenance, selecting the right insulation tape can make a significant difference – a small investment in the right product translates into long-term operational success and safety. As the industry evolves, staying informed about advances in insulation tape technology will continue to be essential for professionals seeking to uphold the highest standards in their work.