Butyl rubber waterproofing has emerged as a game-changer in the construction and renovation industry. Its exceptional properties offer a robust solution for safeguarding structures against the damaging effects of moisture and water ingress. Drawing on years of experience in the field, it's clear that butyl rubber's flexibility, durability, and impermeability make it a preferred choice for a variety of waterproofing applications.
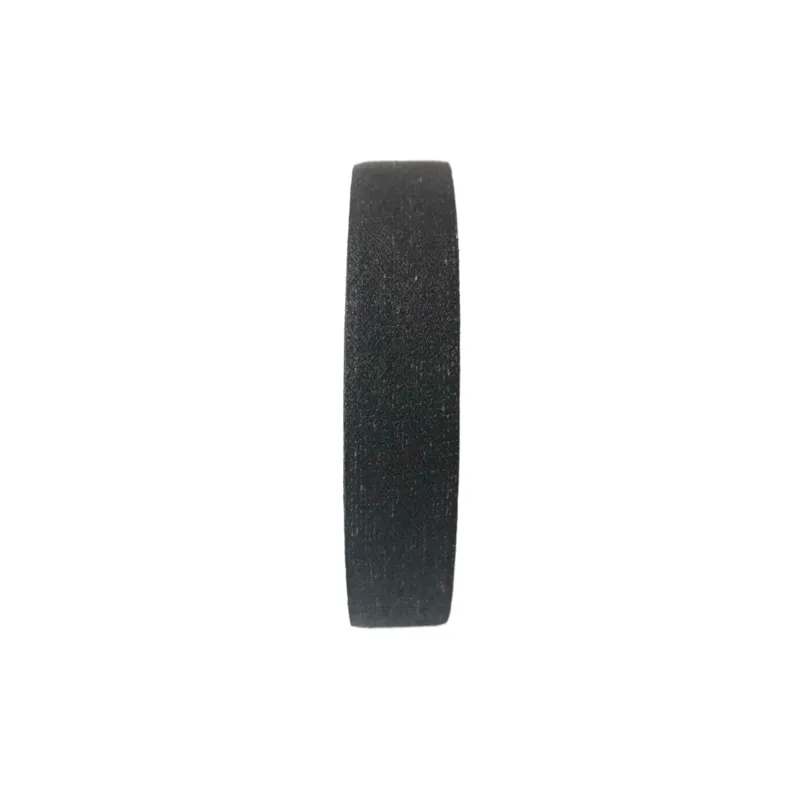
In the realm of waterproofing, expertise is crucial in distinguishing materials that simply perform from those that excel. Butyl rubber stands out due to its unique chemical composition, which combines polyisobutylene with small amounts of isoprene. This blend bestows butyl rubber with an extraordinary ability to retain its flexibility across a wide temperature range while maintaining its watertight integrity. For roofs and facades, where expansion and contraction due to temperature fluctuations are common, this flexibility ensures a consistent seal.
Authoritativeness in construction materials often comes from industry endorsements and long-term performance in rigorous testing environments. Butyl rubber has undergone extensive evaluation, consistently demonstrating resistance to ultraviolet (UV) radiation, ozone, and high temperatures. Unlike some other materials that may degrade or become brittle when exposed to harsh weather conditions, butyl rubber maintains its physical properties, providing a long-lasting and reliable barrier against water.

Trustworthiness is another critical factor when selecting waterproofing materials. Contractors and architects have placed their confidence in butyl rubber for years due to its proven track record. When applied correctly, butyl rubber membranes can last over 20 years, even in challenging conditions, minimizing the need for frequent repairs and reapplications. This trust is reinforced by the warranty packages that often accompany butyl rubber products, offering customers peace of mind regarding their investment.
butyl rubber waterproofing
From a practical standpoint, the ease of application also contributes to butyl rubber’s popularity. It adheres well to a variety of surfaces, including metal, concrete, and wood, without the need for primers in most cases. This adaptability can significantly reduce preparation time and labor costs. Furthermore, its non-toxic nature and low VOC emissions make it an environmentally friendly option that aligns with sustainable building practices.
When considering the total cost of waterproofing a structure, butyl rubber offers competitive advantages. Its durability contributes to a lower lifecycle cost compared to materials that may require more frequent maintenance or replacement. This cost-efficiency becomes particularly evident in large-scale projects, where material longevity can lead to substantial savings.
Butyl rubber is also gaining traction in eco-friendly construction initiatives. Its ability to reduce energy costs through improved insulation and its compatibility with green roofs and other sustainable architectural features make it an appealing choice for those committed to reducing their carbon footprint.
In conclusion, butyl rubber waterproofing provides a compelling solution for both residential and commercial applications. Its combination of flexibility, durability, and environmental compatibility, backed by decades of successful use, makes it a material that both experts and novices alike can trust for effective moisture management. As building practices continue evolving towards more sustainable and efficient methodologies, butyl rubber is well-positioned to remain at the forefront of waterproofing technologies.