Warehouse floor tape is an indispensable tool in the logistics and supply chain industry, serving both functional and safety purposes. As an expert with years of experience in optimizing warehouse operations, I can attest to the critical importance of using the right floor tape to enhance efficiency, safety, and overall operational flow.
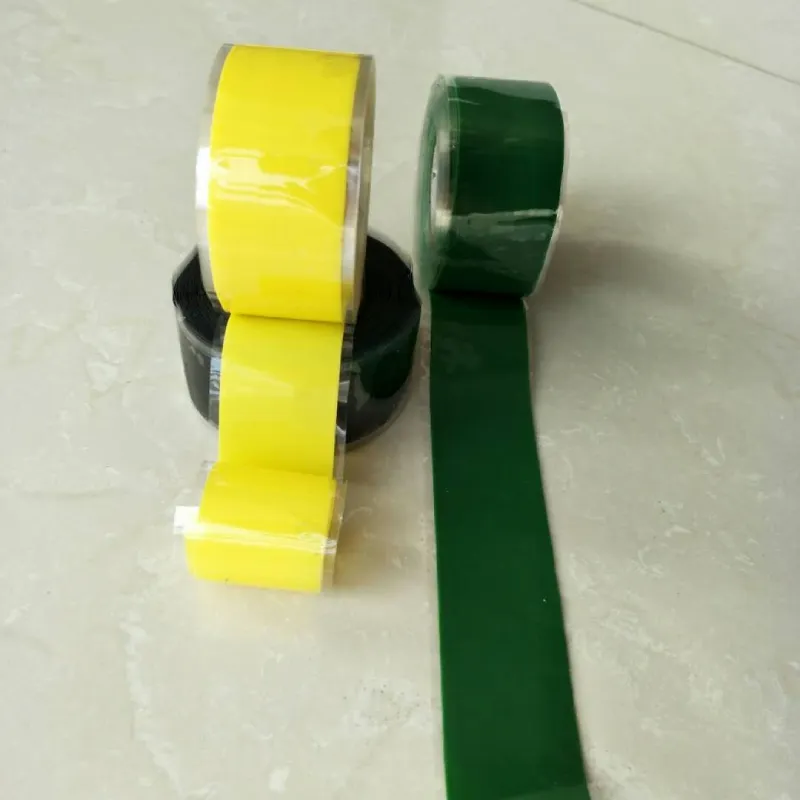
In the bustling environment of a warehouse, where precision and organization are paramount, warehouse floor tape offers a simple yet highly effective solution to manage traffic, delineate work zones, and enforce safety guidelines. Floor tape's versatility in application makes it an authoritative choice for warehouse managers aiming to boost productivity while minimizing risks.
High-quality warehouse floor tapes are designed with durability and visibility in mind. They are manufactured to withstand the wear and tear of constant foot traffic and the movement of machinery such as forklifts, ensuring longevity and reliability. This reliability translates into cost-effectiveness as it reduces the need for frequent replacements and maintenance.
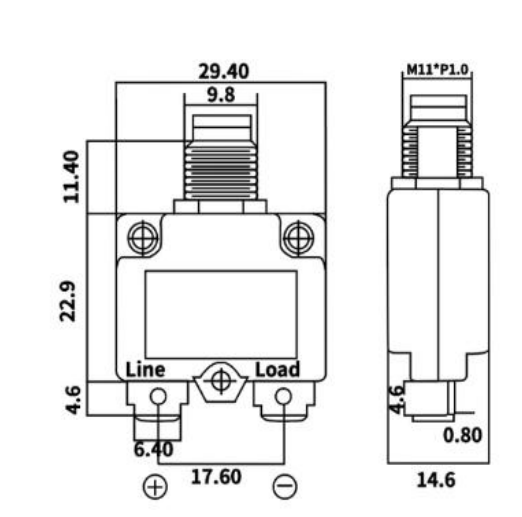
Beyond demarcation, floor tapes enhance trustworthiness as they play a pivotal role in safety compliance. With clear and vibrant colors, warehouse floor tape can signify different zones—such as red for danger areas or yellow for caution—ensuring that safety protocols are visually reinforced. This is crucial in accident prevention and in maintaining a safe working environment. Warehouses that utilize proper floor tape are often seen as more compliant with safety regulations, thereby boosting their authority and credibility in the industry.
The expertise required to select the appropriate tape involves understanding the specific needs of the warehouse environment. For instance, in areas where there might be chemical spills, tapes with chemical resistance are essential. In contrast, areas subjected to extreme temperatures might require specialized heat-resistant tapes. By aligning tape type with environmental conditions, warehouse managers can ensure optimal performance and safety.
warehouse floor tape
Real-world experience shows that effective floor marking systems significantly reduce the time workers spend navigating and organizing their tasks. For example, aisle marking with floor tape allows for quick identification of inventory locations, streamlining the picking process. This increased efficiency not only enhances productivity but also boosts employee morale, knowing that their environment is well-organized and their tasks are clearly outlined.
Additionally, warehouse floor tapes contribute to effective inventory management. By marking storage locations and shipping zones, floor tape can help prevent errors in inventory placement and retrieval. This organizational clarity ensures that operations run smoothly and materials are handled correctly, further enhancing the credibility of the warehouse's logistical capabilities.
Trust in a warehouse's operations can be strengthened by using floor tape to highlight emergency exits and equipment, ensuring quick access in case of an emergency. This practice not only adheres to safety standards but also demonstrates a proactive approach to risk management, reinforcing the trust of employees and external auditors alike.
In conclusion, the strategic application of warehouse floor tape is essential for any facility aiming to optimize its operations while maintaining high safety and compliance standards. Its role in providing clear, organized, and safe environments speaks to the expertise necessary to implement such systems effectively. By selecting and applying floor tape thoughtfully, warehouses can elevate their operational authority, efficiency, and trustworthiness, making them stand out in an industry where these qualities are paramount.